Collect, Analyze and Optimize
Once your processes are in place and your MES system is at work, you can maximize efficiency, yield and quality by collecting and analyzing process data. EZ-MES will allow you to have a seamless integration of your Process Data acquisition, as well as live reports like Product Tracking, WIP and Inventory. This will enable you to make well informed decisions that will improve your bottom line.
Use EZ-MES to collect data
The real time browser based Manufacturing Execution System EZ-MES collects process data as parts travel through different manufacturing steps. Critical travel data such as start time, end time, resources used, yield, drop outs are automatically logged at a very granular level.
Data generated by your manufacturing process can be collected via manual input or in an automated way.
In case of manual data collection, EZ-MES has build-in a number of pre-formated and configurable User Interface elements. Forms using such user interface elements allow seamless input of data by humans while supporting that the date is entered correctly. This is be done by using pre-configured radio buttons, dropdown boxes and input fields with validation checks defined via regular expressions.
Many tools in today's manufacturing environment support data collection, such as barcode-readers, forms, equipment, electronic handheld devices and others. Data generated by those and by equipment using sensors, can be automatically feed to EZ-MES by using its open Application Programming Interface (API). This open API allows software tools for automated measurements to access the data and core functions in EZ-MES.
Analyze collected data
EZ-MES contains a number of pre-formatted reports. For the purpose of data analysis, EZ-MES contains 'out of the box' Statistical Process Control (SPC) Reports. SPC is an industry-standard method for measuring and analyzing data for quality during the manufacturing process. Product, Part and Process measurements are gathered by EZ-MES during manufacturing. This data is then plotted on a graph with pre-determined control limits.
Results that falls within the control limits indicates that everything is operating as expected. Any variation within the control limits is considered to be acceptable due to natural variation in the manufacturing processes. If data consistently falls outside of the control limits, then this indicates that something within the process is likely not running as it is supposed to do. Repairs need to fix the issue before serious defects and possible escalations occur.
Optimize your processes
The immediate and real time use of production data collection and analyses is to detect acute production problems or even faults leading to expensive recalls, if not detected in time. Next to this short term need, there is an obvious and on-going mid- and long term need to further improve both processes and products and reduce costs.
As manufacturing processes are soft configured in EZ-MES instead of being hard-coded, rapid prototyping changes in EZ-MES is relative fast and easy to do, as no programming skills are needed. EZ-MES has an optional Sandbox version which allows you to first try out and simulate changes in your manufacturing processes and in your vertical and horizontal integration of flows. You can dry-run these changes and if accepted, make them available to the Live version of your EZ-MES application. As EZ-MES is a realtime browser application, your changes are immediately deployed to all users, without any need for local software updates.
After the deployment of the changes, you can start collecting and analyzing production data. To evaluate the real world impact of the changes you made.
Screenshots
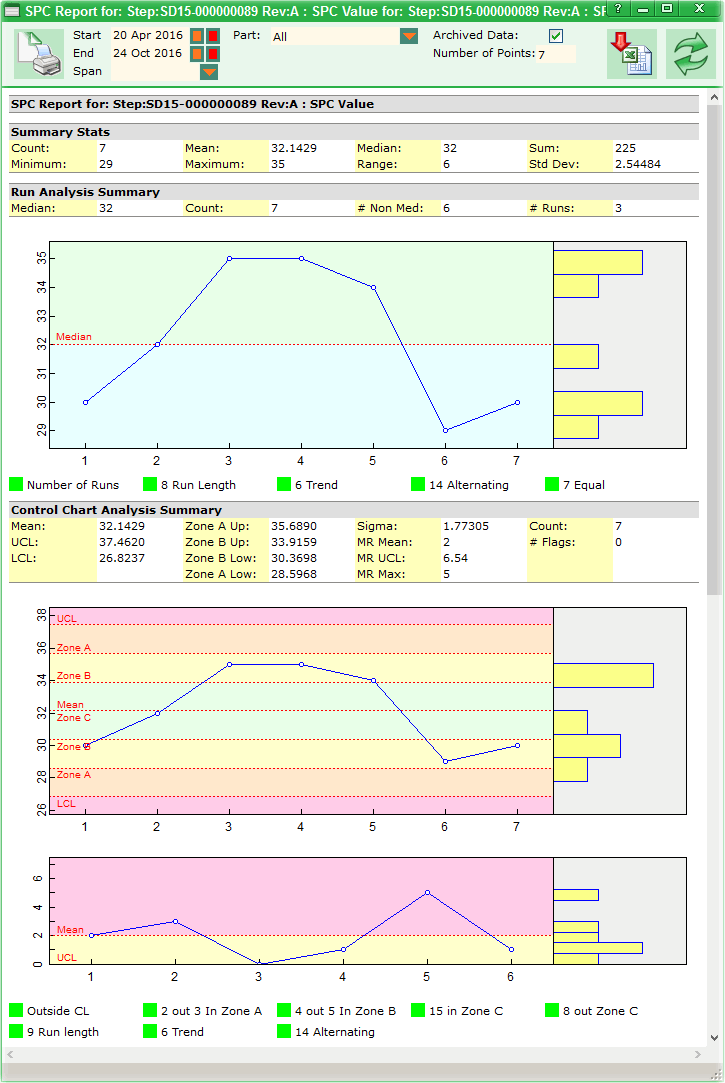
Example of a configurable SPC Report in EZ-MES